Daiwa Lease—the Prefabricated Industrial Buildings Business and Retail Facility Leasing BusinessConvenience store, reusing 90% of building materials for its new stores
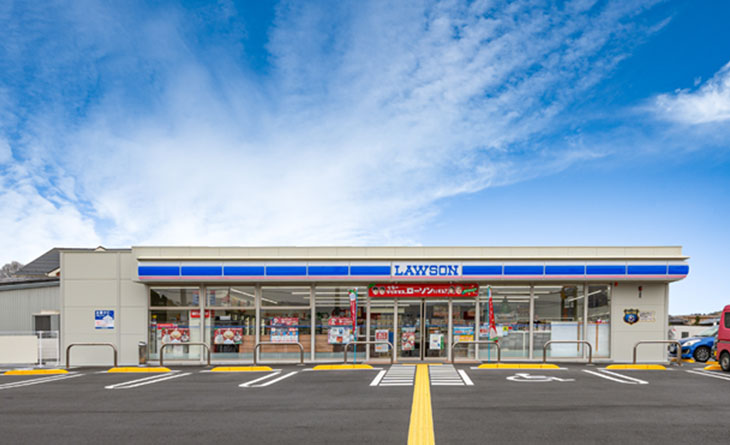
Daiwa Lease Co., Ltd., in collaboration with Lawson, Inc., is proceeding with an endeavor to take building materials from Lawson’s closed stores, such as roofs, walls, pillars, beams, and window sashes, and to reuse them in its new stores. This partnership that the two companies have undertaken has created a sustainable business model that contributes to carbon neutrality and the development of a circular economy. Daiwa Lease is tackling the challenges of a new era while continuing the tradition of its proprietary business model, namely prefabricated construction and building leasing that began with the “Pipe House,” the founding product and origin of the Daiwa House Group.
Overview
Overview of closed store
- Store name :
- Lawson Tsuyama Zaimokumachi Store
- Location :
- Zaimokumachi, Tsuyama City, Okayama Prefecture
- Single-storied building :
- 198.25m2
Overview of new store for parts reuse
- Store name :
- Lawson Tsuyama Takanoyama-nishi Store
- Location :
- Takanoyama-nishi, Tsuyama City, Okayama Prefecture
- Single-storied building :
- 198.25m2
Approximately 90% of building materials are reused
On a by-weight basis, approximately 90% of the building materials (roofing, walls, columns, beams, window sashes, etc.) used in the frame and exterior wall sections of the closed store are reused.
CO2 emissions cut by 60%
Expectations are for CO2 emissions, from material production to completion of the building, to be reduced by approximately 60%, as compared to a regular store.
Costs cut by 30%
An approximately 30% cost reduction in the building frame portion (foundation, steel frame, exterior walls, roofing, window sashes).
Flow for reuse
Step 1. Closure
Advance survey for reusability
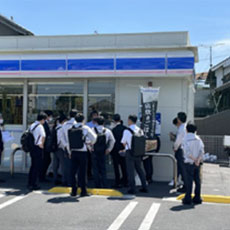
Daiwa Lease supports Lawson in establishing stores across Japan. This is especially true for the construction of roadside stores, for which the “DL-e construction method” was jointly developed in 2013, and adopted by more than a few stores. This method enables uniform construction standards for stores throughout Japan, and developed into an initiative for resource recycling.
With regard to parts reuse, after confirming various conditions such as the specifications of the closed store, the area in which the new store will be opened, and the time span between closure and opening of the stores, Daiwa Lease makes a comprehensive decision on whether the building materials can be reused for the new store, taking into account the cost of transportation.
Point
What is the DL-e construction method which unites Lawson and Daiwa Lease?
DL-e construction is a prefabricated method of construction that uses lightweight steel frames. When the Great East Japan Earthquake hit in 2011, Daiwa Lease had been in charge of constructing temporary stores that were easy to put together and disassemble in order to resume store operations as quickly as possible in the affected areas. This is what gave rise to the DL-e construction method. From 2013, Lawson adopted this method for its standard stores across Japan, and a total of roughly 3,500 have been shipped. This construction method, in which designated modularized building materials are assembled on site, is characterized by ease of assembly and disassembly. Therefore, from the beginning of development, Daiwa Lease has been designing products with a view to reusing building materials, and has also been improving construction methods.
Step 2. Disassembly
Careful dismantling of building materials, one by one, in accordance with demolition standards
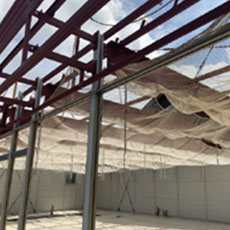
At Lawson stores, building materials such as roofing, walls, pillars, beams, and window sashes are targets for reuse. The company’s specialized subcontractors carefully and individually dismantle building materials based on the dismantling standards and expertise Daiwa Lease has accumulated through its leasing business. Considering the impact of sunlight’s ultraviolet rays and other factors, visual innovations such as labeling exterior panels so that they can be reassembled in the same position at the store that reuses them is among the ways the baton will be passed on to the next step.
Although only building materials are subject to this kind of reuse, Daiwa Lease is also actively involved in the reuse of foundation materials in its leasing business and upcycling of used exterior walls for leasing.
Point
What is “system construction” that simplifies reuse?
This is a building construction method that standardizes the shapes, dimensions, and joining methods of components that make up buildings, and which systematizes all design and construction processes. The use of standardized components and parts helps reduce costs in the procurement and manufacturing stages while maintaining high quality, and also shortens construction lead times as assembly can be performed quickly on site. Daiwa Lease delivers exceptionally reliable products under strict quality control through its consistency, from materials procurement to processing and assembly at its own factories. In addition, it has established a highly flexible production and logistics system that includes rapid transport, after-sales care, and maintenance with a focus on depots and plants throughout Japan, thus further shortening construction lead times and reducing costs.
Step 3. Maintenance
Maintenance at depots and factories according to standards developed for each component
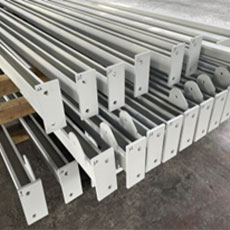
The first stop for dismantled building materials is at one of the depots or factories located around Japan. At such depots, which serve as distribution centers for Daiwa Lease’s building reuse system, high quality is maintained for the maintenance of building materials, independent of the skill level of the workers, based on the management standards for parts and materials. Moreover, headquarters updates standards on an as-needed basis.
Given that the building materials to be reused at stores are Lawson-held assets, the scope of maintenance will be determined based on the management standards established by Daiwa Lease, while comprehensively considering various factors such as safety, quality, and appearance.
Point
Maintenance for ongoing, long-term protection of safety and security
Daiwa Lease’s standardized products, chiefly with the DL-e construction method, have established criteria for sorting parts for reuse and management standards for maintenance. Based on these standards, the company supplies safe and secure parts through sorting, maintenance, and shipping.
The Shikoku depot and factory
Applying rust prevention coating and making repairs
Step 4. Rebuilding
At a new site, the same process as for new parts
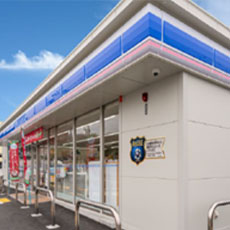
After maintenance has been completed, building materials are delivered to the new construction site and transformed into a new store, using the same process and in the same time frame as if all the materials were brand new. On the other hand, those building materials that have failed to satisfy reuse standards based on the results of inspections and maintenance are replaced with new items.
Reusing parts contributes to reduced burden on the living environment by controlling noise, vibration, and dust during construction and demolition, as well as by reducing CO2 emissions.
Point
Creating new value by “not over-maintaining"
Even if there are stains or small dents on exterior walls or construction materials, we do not replace them with new ones or perform excessive maintenance as long as there are no quality problems. In principle, we reuse usable materials to reduce environmental impact. In addition, LAWSON's unique reuse stickers are placed on the exterior walls of stores to promote the environmental value of reused stores to customers who use them.
Voice of the Person in Charge
We were convinced that this would be better for the customer and for society, and have been moving forward on this initiative through countless discussions with Lawson. Bringing this initiative to reality is, we believe, owing to our constant communication and relationship of trust that we’ve had with Lawson over the years.
There’s been a huge volume of feedback from both in and outside of the company! Not only does this initiative cut CO2 emissions, but we can keenly feel the range of positive impacts, including reductions in environmental burden during construction, solutions to a wide array of environmental issues such as the creation of a circular economy, as well as to problems faced by customer issues such as cost reduction.
Daiwa Lease Co., Ltd.
Head office
Deputy General Manager, Design Promotion Dept.
Masaki Inukai
The “Pipe House,” the founding product of the Daiwa House Group. The expertise that arose from such systemized construction is a part of this current project, and with that we feel proud to be recognized for our aspirations and corporate values “to do things because they will be of service to society.” Properly managing a wide variety of building materials scattered across the country is certainly a labor intensive task, but we are going forward with our heads held high based on our ability to provide products that satisfy our customers by utilizing the know-how we have cultivated over the years.
Daiwa Lease Co., Ltd. (from right)
- Seiji Kita, General Manager, Production and Depot Promotion
- Yasutaka higashi, Depot Manager, Okayama Deport, Hiroshima Depot, and Shikoku Depot
- Keiko Kuroda, Chief, Asset Management Group, Shikoku Depot
- Ryoko Ooe, Production Management Group, Shikoku Depot
* The information is current at the time of interviews (Dec. 2024).